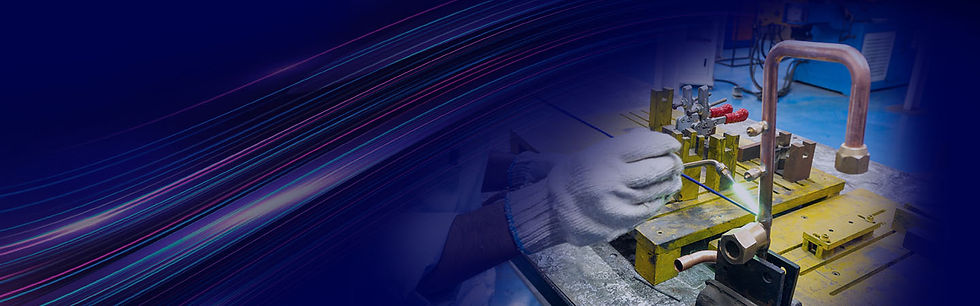
Friguss
HVAC
Friguss - HVAC stands as a cornerstone in the HVAC (Heating, Ventilation, and Air Conditioning) industry, renowned for its unwavering commitment to innovation, quality, and customer satisfaction. With decades of experience, our company has solidified its position as a trusted manufacturer and fabricator of essential components for HVAC systems.
-
Friguss - HVAC specializes in the design and manufacturing of sheet metal enclosures tailored for HVAC systems, including chiller units and various other air conditioning equipment. These enclosures are meticulously crafted to provide structural integrity, thermal insulation, and protection for critical HVAC components.
-
-
We excel in the production of sheet metal dampers, vital components that regulate airflow within HVAC systems. Our dampers are engineered with precision to ensure optimal performance, energy efficiency, and comfort control in diverse environmental conditions.
-
-
Friguss - HVAC is at the forefront of tube fabrication, offering expertise in both copper and stainless steel tubing solutions for industrial air conditioning systems. From CNC bending to brazing, our fabrication process incorporates cutting-edge technologies and stringent quality controls to deliver superior products that meet the highest industry standards.
-
In addition to our core offerings, Friguss - HVAC manufactures high-quality insulation materials designed specifically for HVAC applications. Our insulation solutions are engineered to enhance energy efficiency, minimize heat transfer, and optimize system performance. Whether for ductwork, pipes, or equipment enclosures, our insulation products provide superior thermal protection and contribute to overall system reliability and efficiency.
Our Specializations:
Each step is meticulously executed by our skilled technicians and engineers to ensure the reliability, durability, and performance of the final products.
Quality Assurance: At Friguss - HVAC, quality is ingrained in every aspect of our operations. We maintain strict adherence to industry regulations and standards, backed by comprehensive quality control measures at every stage of production. Our commitment to excellence extends beyond mere compliance, as we continuously strive to exceed customer expectations and set new benchmarks for quality in the HVAC industry.
Friguss - HVAC boasts state-of-the-art CNC tube bending capabilities, allowing for precise manipulation of tube geometry to meet exact specifications.
Equipment Capacity: Our CNC tube bending machinery accommodates tube diameters ranging from 6.35 mm to 70 mm, offering versatility to cater to a wide range of applications.
Precision Engineering: Utilizing advanced computer-controlled technology, our CNC tube bending process ensures consistent accuracy and repeatability, resulting in uniform bends with minimal distortion.
Customization: Whether it's complex shapes, tight radii, or specific angles, our CNC tube bending equipment enables the fabrication of custom tube configurations tailored to the unique requirements of each HVAC system.
Quality Control: Each bent tube undergoes rigorous inspection to verify dimensional accuracy and adherence to design specifications, ensuring optimal fit and functionality within the HVAC system.
CNC Tube Bending
-
Friguss - HVAC employs various tube forming techniques to shape and manipulate metal tubing according to project requirements.
-
Methodologies: Our tube forming capabilities encompass a range of methodologies, including flaring, swagging, spinning and other specialized techniques, selected based on factors such as material properties, geometrical complexity, and production volume.
-
Material Compatibility: Whether working with copper or stainless steel tubes, our tube forming processes are tailored to accommodate the unique characteristics of each material, ensuring integrity and performance throughout fabrication.
-
Flexibility: From simple bends to intricate profiles, our tube forming capabilities offer unparalleled flexibility, allowing for the creation of diverse tube configurations to suit the demands of various HVAC applications.
Tube Forming
-
Brazing plays a crucial role in joining metal components within HVAC systems, ensuring strong and durable connections that withstand the rigors of operation.
-
Process Expertise: Friguss - HVAC employs skilled technicians proficient in the art of brazing, utilizing advanced techniques and equipment to achieve robust bonds between tube segments and other components.
-
Material Compatibility: Whether brazing copper or stainless steel tubes, our process parameters are meticulously controlled to optimize joint integrity and minimize the risk of defects such as leaks or weak spots.
-
Quality Assurance: Each brazed joint undergoes stringent inspection and testing to verify structural integrity and adherence to quality standards, ensuring reliability and performance in demanding HVAC environments.
-
Safety Considerations: Our brazing operations adhere to industry best practices and safety protocols to mitigate risks associated with high-temperature processes, safeguarding both personnel and equipment throughout fabrication.
Brazing
-
High-pressure testing is a critical step in validating the integrity and reliability of fabricated tube assemblies, ensuring they can withstand the operating conditions encountered in HVAC systems.
-
Testing Equipment: Friguss - HVAC is equipped with advanced pressure testing facilities capable of subjecting fabricated tube assemblies to pressures ranging from 0 to 530 PSI (pounds per square inch).
-
Quality Assurance: Prior to installation, each tube assembly undergoes thorough pressure testing to verify its resistance to internal pressures, leakage, and other performance parameters.
High-Pressure Testing
-
The assembly phase brings together fabricated tube components and other HVAC system elements to create functional assemblies ready for installation.
-
Precision Integration: Friguss - HVAC's assembly processes prioritize precision and accuracy, ensuring seamless integration of fabricated tubes, enclosures, dampers, and other components to form cohesive HVAC subsystems.
-
Quality Checks: Each assembled unit undergoes comprehensive inspection and testing to verify proper fit, alignment, and functionality, addressing any discrepancies or deficiencies before deployment in the field.
-
Final Validation: Prior to shipment, assembled HVAC subsystems undergo final validation tests to confirm performance parameters such as airflow, temperature control, and system efficiency, assuring reliability and compliance with project specifications.
-
Packaging and Delivery: Assembled units are carefully packaged to prevent damage during transit and delivered to the customer's site according to agreed-upon schedules, ensuring timely completion of HVAC installations and project milestones.
Assembly
Fabrication Process
Our fabrication process is characterized by precision and efficiency, encompassing various stages including